Introduction
Pad printing technology has revolutionized the way intricate designs are transferred onto various surfaces. From high-precision electronics to customized promotional items, the ability to handle complex and multi-color designs is crucial for many industries. This article aims to guide potential buyers in understanding how pad printing machines, or pad printers, manage these intricate requirements and what to consider when selecting a machine suited for complex prints.
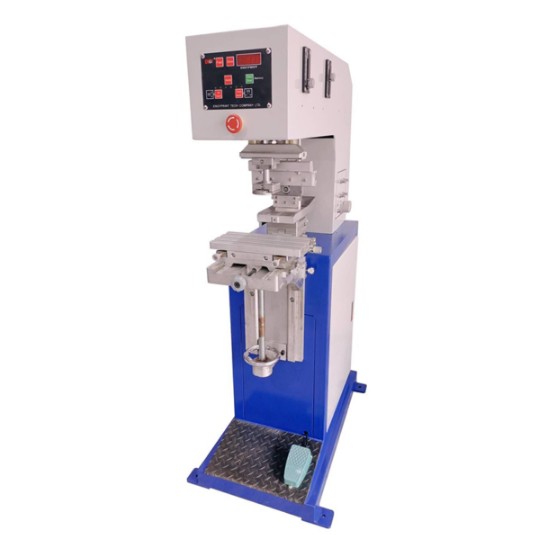
Understanding Pad Printing Technology
Overview of Pad Printing
Pad printing is a versatile printing technique that utilizes a silicone pad to transfer ink from an etched plate onto a substrate. This method is highly valued for its ability to print on uneven surfaces and intricate details. The primary components of a pad printing machine include:
- Pad: Transfers the ink from the plate to the substrate.
- Plate: Holds the design, which is transferred to the pad.
- Substrate: The surface onto which the design is printed.
The flexibility and precision of pad printing make it an excellent choice for handling complex and multi-color designs. Unlike other printing methods, pad printing allows for detailed and consistent reproduction of intricate patterns and vibrant colors.
Why Pad Printing is Suitable for Complex Designs
One of the key advantages of a pad printing machine is its capability to handle detailed designs with multiple colors. The process involves several stages that ensure high accuracy and quality:
- Multi-Color Printing Capabilities: Pad printing machines can achieve multi-color designs through the use of multiple plates and color stations. Each plate corresponds to a specific color, and the design is built up layer by layer.
- Registration and Alignment: Accurate registration of each color is crucial for maintaining design integrity. Pad printers are equipped with precise alignment mechanisms to ensure that colors overlap correctly and that the final design is true to the original artwork.
The advanced technology used in pad printing supplies and equipment contributes significantly to the ability of pad printing machines to manage complex and multi-color designs effectively.
Key Features for Handling Complex Designs
Multi-Color Printing Capabilities
Pad printing machines are specifically designed to handle multi-color designs, a feature essential for producing high-quality and intricate prints. This capability is achieved through several mechanisms:
- Multiple Plates: Each color in a design is printed using a separate plate, allowing for precise layering of colors. The plates are engraved or photopolymerized with the design elements for each specific color.
- Color Stations: Advanced pad printers may have multiple color stations, where each station applies a different color in sequence. This setup ensures that each color is applied accurately and that the final print is vibrant and detailed.
By using these features, pad printing machines can reproduce complex designs with multiple colors consistently, making them a valuable tool for industries that require detailed and colorful prints.
Registration and Alignment
Proper registration and alignment are critical when printing complex and multi-color designs. Misalignment can lead to color blurring and a loss of design accuracy. Pad printing machines address these issues through:
- Precise Registration Mechanisms: High-quality pad printers are equipped with advanced registration systems that ensure each color plate is aligned correctly with the others. This precision is crucial for maintaining the integrity of intricate designs.
- Adjustable Alignment Settings: Many pad printing machines offer adjustable settings to fine-tune the alignment of each color layer. This flexibility helps accommodate different design complexities and substrates.
Accurate registration and alignment are essential for achieving a professional and high-quality finish on complex prints.
Plate Technology
The plate used in a pad printing machine is a vital component that influences the quality of the final print. Several plate technologies are available, each offering distinct advantages:
- Laser-Engraved Plates: These plates are created using laser engraving, which provides high precision and detail for complex designs. Laser-engraved plates are known for their durability and consistency.
- Chemical etching Plates: Made by etching machine with chemical etching, the whole plate making process is complicated but the printing results is very good.
Choosing the right plate technology depends on the specific requirements of the design and the desired quality of the print. Each type of plate has its benefits, and understanding these can help users select the best pad printing supplies for their needs.
The Role of Ink Systems
Ink Compatibility
The choice of ink plays a significant role in handling complex and multi-color designs with pad printing machines. Different types of inks are available, each offering unique benefits:
Solvent-Based Inks: These inks are versatile and widely used in pad printing. They offer excellent adhesion to various substrates and are suitable for designs requiring vibrant colors and fine details.
UV-Curable Inks: UV-curable inks are known for their quick drying times and durability. They cure instantly under UV light, making them ideal for high-speed production environments and intricate designs.
Choosing the right ink type is crucial for achieving the desired color quality and ensuring that the design is faithfully reproduced. Compatibility with the substrate and the specific requirements of the design must be considered when selecting pad printing supplies.
Ink Application and Control
Effective control of ink application is essential for maintaining the quality of complex and multi-color prints:
Ink Thickness and Consistency: The thickness and consistency of the ink can impact the final design. Pad printing machines are equipped with systems to regulate ink viscosity and ensure even application across different colors.
Ink Viscosity: Proper ink viscosity is necessary for achieving accurate color reproduction and preventing issues such as bleeding or smudging. Adjusting the viscosity allows for better control over the print quality.
By managing ink application and viscosity, pad printers can produce detailed and precise prints that meet the requirements of complex designs.
Machine Specifications and Technology
Automatic vs. Manual Machines
When selecting a pad printing machine for handling multi-color designs, it’s important to consider the type of machine that best suits your needs:
Automatic Machines: These machines offer advanced features and automation for high-volume production. They typically include multiple color stations, and programmable settings for consistent results.
Manual Machines: Manual pad printers are more cost-effective and may be suitable for smaller production runs. However, they require more operator intervention and may not offer the same level of precision and efficiency as automatic models.
For complex and multi-color designs, automatic pad printing machines are often preferred due to their ability to handle intricate tasks with high precision and reduced manual effort.
Advanced Features for Complex Printing
Modern pad printing machines come equipped with several advanced features that enhance their ability to handle complex designs:
Touchscreen Controls: Many machines feature intuitive touchscreen interfaces that simplify operation and allow for precise adjustments of settings.
Programmable Settings: Advanced models offer programmable settings for color changes, registration adjustments, and design specifications, making it easier to manage complex and multi-color prints.
Integration with Design Software: Some pad printers can be integrated with design software to ensure that the final print matches the original artwork accurately.
These features contribute to the efficiency and accuracy of pad printing machines, making them well-suited for handling intricate and multi-color designs.
Challenges and Solutions
Common Issues with Multi-Color Pad Printing
Despite the advantages of pad printing machines, there are common challenges when handling multi-color designs:
- Color Registration Problems: Achieving precise color alignment can be difficult, especially with complex designs. Misalignment may result in blurry or inconsistent colors.
- Ink Adhesion Issues: Different inks and substrates can affect how well the ink adheres, leading to problems with durability and color fidelity.
- Design Fidelity: Maintaining the integrity of intricate designs throughout the printing process can be challenging, particularly when transitioning between colors or substrates.
Addressing these challenges requires understanding the specific needs of the design and the capabilities of the pad printing machine.
Troubleshooting Tips
To overcome these issues, consider the following troubleshooting tips:
- Regular Calibration: Ensure that the pad printing machine is regularly calibrated to maintain accurate color registration and alignment. This helps in reducing misalignment issues.
- Proper Ink Selection: Choose the appropriate ink type for the substrate and design requirements. Conduct tests to ensure good adhesion and color quality.
- Maintenance and Cleaning: Regular maintenance and cleaning of the machine components, such as pads and plates, help prevent problems and ensure consistent print quality.
Implementing these practices can enhance the performance of pad printing machines and improve the quality of complex and multi-color prints.
Case Studies and Examples
Successful Multi-Color Projects
Pad printing machines have been successfully used in various industries to produce complex and multi-color designs:
- Electronics: High-precision electronics often require intricate designs and multi-color markings. Pad printing machines are used to apply detailed graphics and labels on electronic components.
- Promotional Products: Custom promotional items, such as branded pens and mugs, frequently feature complex designs and vibrant colors. Pad printers handle these requirements with ease, producing high-quality, eye-catching products.
Real-World Applications
Several businesses have leveraged pad printing machines for intricate designs:
- Aerospace Industry: Aerospace components often feature multi-color markings for identification and functional purposes. Pad printing machines are used to ensure these markings are clear and durable.
- Medical Devices: Medical devices may require detailed and precise labeling for compliance and usability. Pad printing machines help achieve the necessary level of detail and accuracy.
These examples highlight the versatility of pad printing machines in handling complex designs and multi-color applications across various industries.
Choosing the Right Pad Printing Machine
Factors to Consider
When selecting a pad printing machine for complex and multi-color designs, consider the following factors:
- Machine Size and Capacity: Evaluate the size and production capacity of the machine to ensure it meets your needs. Larger machines may be required for high-volume production, while smaller machines may suffice for smaller runs.
- Design Requirements: Assess the complexity and color requirements of your designs. Choose a machine that offers the necessary color stations, registration accuracy, and plate technology.
- Budget and Cost: Determine your budget and consider the total cost of ownership, including the purchase price, maintenance, and operational costs. Investing in a high-quality machine may offer better long-term value.
Recommended Models
Several pad printing machines are well-suited for handling complex and multi-color designs:
- Model A: Features advanced registration systems and multiple color stations, making it ideal for intricate and high-volume applications.
- Model B: Offers flexible plate options and programmable settings, providing versatility for various design requirements.
- Model C: Known for its precision and ease of use, suitable for businesses needing reliable performance for multi-color prints.
Consulting with experts and reviewing product specifications can help you choose the best pad printing machine for your needs.
Conclusion
Pad printing machines are essential tools for producing complex and multi-color designs with high precision and quality. Understanding how these machines handle intricate prints, from plate technology to ink systems and advanced features, can guide you in selecting the right equipment for your business. By considering factors such as machine capabilities, design requirements, and budget, you can make an informed decision and invest in a pad printing machine that meets your needs.
Whether you are in electronics, promotional products, or any other industry requiring detailed and vibrant prints, a well-chosen pad printing machine will enhance your production capabilities and ensure that your designs are accurately and consistently reproduced.