Introduction
Pad printing is a versatile process that transfers 2D images onto 3D objects. This technique is widely applied in various industries, including automotive, medical devices, electronics, and promotional products. The process involves using a silicone pad to pick up ink from an etched plate and then transferring it onto the substrate. A critical aspect of achieving high-quality prints is the surface treatment of the substrate before printing. Surface treatments enhance ink adhesion and durability, ensuring the prints remain vibrant and long-lasting.
This article aims to provide potential buyers of pad printing machines with detailed information about different surface treatments. By understanding these treatments, buyers can make informed decisions and choose the right pad printing equipment that meets their needs.
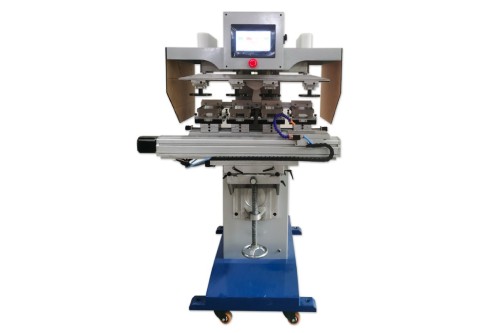
Types of Pad Printing Surface Treatments
Corona Treatment
Description:
Corona treatment involves applying a high-frequency electrical discharge to a material’s surface. This process increases the surface energy, making it more receptive to ink adhesion.
Applications:
Corona treatment is particularly effective for non-conductive surfaces such as plastics. It is commonly used in industries where high-quality, durable prints are required on plastic substrates.
Benefits:
- Improves ink adhesion
- Enhances print quality
Considerations:
- Cost implications
- Equipment requirements
Flame Treatment
Description:
Flame treatment exposes the material’s surface to a gas flame. This exposure oxidizes the surface, increasing its energy and improving ink adhesion.
Applications:
This treatment is widely used for polyolefin materials, such as polyethylene (short name as PE)commonly found in various packaging and automotive components.
Benefits:
- Increases surface energy
- Ensures better ink adherence
Considerations:
- Safety measures
- Training requirements
Plasma Treatment
Description:
Plasma treatment utilizes ionized gas to modify a material’s surface properties. This process can be tailored to treat various materials, including metals, glass, and plastics.
Applications:
Effective on diverse substrates, plasma treatment is ideal for industries that require uniform and high-quality surface modification.
Benefits:
- Provides uniform treatment
- Environmentally friendly option
Considerations:
- Initial investment costs
- Maintenance needs
Mechanical Abrasion
Description:
Mechanical abrasion is a physical method of roughening the surface using abrasive materials. This treatment is straightforward and cost-effective, making it suitable for various applications.
Applications:
Suitable for metals and rigid plastics, mechanical abrasion is commonly used in industries where robust and durable prints are essential.
Benefits:
- Simple and cost-effective
- Enhances ink adhesion
Considerations:
- Consistency of treatment
- Potential for surface damage
Factors to Consider When Choosing a Surface Treatment
Material Compatibility
Selecting the proper surface treatment depends on the substrate material. Matching the treatment to the material is crucial to ensure optimal ink adhesion and print quality.
Desired Print Quality
The level of detail and durability required in the prints should guide the choice of surface treatment. Different treatments offer varying degrees of adhesion and longevity.
Production Volume
Consider the treatment method’s scalability based on the production volume. High-volume production might require faster and more efficient treatments.
Cost and Budget
Balance the upfront costs of the surface treatment equipment with the long-term benefits. Investing in the right pad printer and surface treatment can save costs in the long run.
Environmental and Safety Concerns
Ensure that the chosen surface treatment complies with environmental regulations and safety standards. Proper handling and disposal of chemicals and equipment are essential for a safe working environment.
Conclusion
Choosing the proper surface treatment is crucial for achieving high-quality prints with a pad printing machine. Each type of surface treatment—corona treatment, flame treatment, plasma treatment,and mechanical abrasion—offers unique benefits and considerations. Understanding these treatments can help users select the most appropriate method.
When purchasing a pad printing machine, it’s essential to consider the compatibility of surface treatments with the substrates you plan to print on. Ensure that the pad printing equipment can accommodate the necessary surface treatments. Consulting with manufacturers and industry experts can provide valuable insights into the best practices for your printing needs.