The unsung hero of consistent, high-quality pad printing is often the humble doctoring ring within your ink cup. This seemingly small component plays a critical role in ensuring the precise amount of ink is deposited onto the printing plate, directly influencing the clarity and sharpness of your final product. When it comes to choosing this vital component, the debate often boils down to two formidable materials: carbide and ceramic. But which one is truly best for your pad printing ink cup? This article will delve deep into the properties, advantages, and disadvantages of each, helping you make an informed decision that elevates your printing operations.
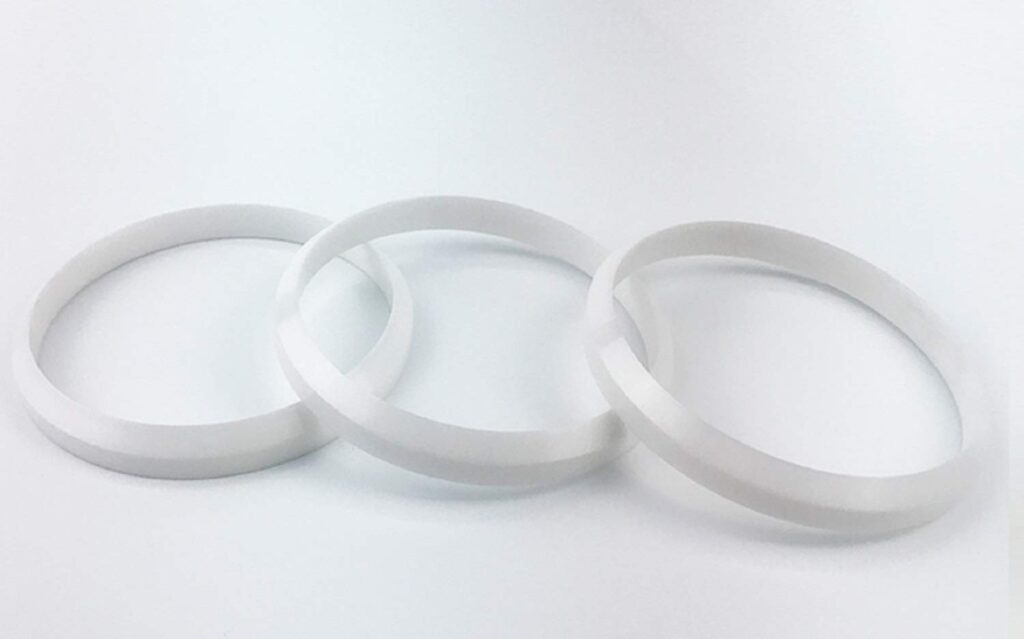
Understanding Carbide Rings
Carbide rings, specifically those made from tungsten carbide, are engineered for extreme performance. This composite material is created by combining tungsten (a hard metal) with carbon, resulting in a material renowned for its exceptional properties.
Material Composition & Properties
Tungsten carbide is lauded for its extraordinary hardness, often measured on the Vickers scale, where it significantly outperforms most steels. This inherent hardness translates directly into superior wear resistance and high rigidity, making it incredibly resilient against the constant friction of the printing process. Its excellent abrasion resistance ensures it can withstand the wear from even the most abrasive inks, such as those containing metallic flakes or ceramic pigments.
Advantages of Carbide Rings
The benefits of integrating a Carbide Ring For Pad Printing Ink Cups into your setup are substantial:
- Unmatched Durability & Longevity: This is perhaps the most significant advantage. Carbide rings boast a significantly extended lifespan compared to ceramic or traditional steel rings. In high-volume production environments, this means fewer ring changes, leading to less downtime and increased productivity.
- Superior Print Quality & Consistency: The extreme hardness of carbide allows for unparalleled doctoring precision. This precise wiping action ensures a perfectly clean plate with each print cycle, resulting in sharper images, finer details, and fewer print defects like hazing or ghosting. For industries demanding meticulous detail, such as medical device printing or intricate electronics, the consistency offered by a Carbide Ring For Pad Printing is invaluable.
- Reduced Downtime & Maintenance: The longer life of carbide rings directly translates to less frequent maintenance. Operators spend less time replacing worn rings and more time producing, thereby optimizing overall operational efficiency.
- Compatibility with Abrasive Inks: If your applications involve highly pigmented, metallic, or ceramic inks, carbide rings are the clear winner. Their robust nature means they can withstand the abrasive particles in these inks without degrading quickly, maintaining their precise doctoring edge for longer.
Disadvantages of Carbide Rings
While highly effective, carbide rings do have some considerations:
- Higher Initial Cost: The manufacturing process for carbide rings is more complex and specialized, leading to a higher upfront investment compared to ceramic options.
- Brittleness (Susceptibility to Chipping/Cracking): Despite their extreme hardness, carbide rings can be brittle. This means they are susceptible to chipping or cracking if mishandled, dropped, or subjected to sudden impacts. Careful handling during installation and cleaning is crucial.
- Weight: Carbide rings are heavier than ceramic, which can be a minor consideration for some automated systems or specific handling requirements.
Understanding Ceramic Rings
Ceramic rings, typically composed of zirconium oxide, represent another strong contender in the ink cup doctoring arena. They offer a compelling balance of performance and cost-effectiveness.
Material Composition & Properties
Zirconium oxide ceramics are known for their high hardness, though generally less than that of tungsten carbide. They offer good wear resistance and excellent corrosion resistance, making them suitable for use with various ink formulations. Their lighter weight can also be an advantage in certain applications.
Advantages of Ceramic Rings
Ceramic rings offer several compelling benefits:
- Lower Initial Cost: For budget-conscious operations or those with lower production volumes, ceramic rings present a more affordable initial investment.
- Good Wear Resistance: Compared to traditional steel doctoring blades, ceramic rings offer significantly improved wear resistance, leading to a longer operational life.
- Corrosion Resistance: Their chemical inertness makes them highly resistant to corrosion from various solvents and ink components, which can be beneficial for certain specialized inks.
- Lighter Weight: Ceramic rings are lighter than their carbide counterparts, which can be advantageous in systems where weight is a factor.
Disadvantages of Ceramic Rings
Despite their advantages, ceramic rings have certain limitations:
- Shorter Lifespan than Carbide: Under identical operating conditions, ceramic rings will generally wear out faster than carbide rings, especially in high-volume production or with abrasive inks.
- Lower Resistance to Abrasive Inks: While better than steel, ceramic rings can show signs of wear quicker when exposed to highly pigmented or abrasive inks, potentially leading to more frequent replacements.
- Susceptibility to Breakage: Ceramic is inherently more prone to catastrophic failure (shattering) upon sudden impact compared to carbide, requiring careful handling.
Key Comparison Factors: Carbide vs. Ceramic
To truly understand which material is best, let’s conduct a head-to-head comparison across critical performance indicators:
Feature | Carbide Rings | Ceramic Rings |
Durability & Lifespan | Exceptional; significantly longer lifespan (e.g., 2-5x or more than ceramic) due to extreme hardness. | Good; offers improved lifespan over steel, but shorter than carbide in demanding applications. |
Print Quality | Superior precision and consistency, leading to sharper prints and fewer defects over extended runs. | Good precision, but may show subtle degradation in consistency or sharpness over time more quickly than carbide. |
Initial Cost | Higher upfront investment. | Lower upfront cost. |
Long-Term Cost | Lower operational cost due to reduced downtime, fewer replacements, and consistent print quality. | Higher operational cost in high-volume setups due to more frequent replacements. |
Abrasive Ink Resistance | Excellent; highly resistant to wear from abrasive pigments. | Good; can show wear quicker with highly abrasive or metallic inks. |
Chipping/Breakage | High hardness but brittle; susceptible to chipping if dropped or impacted. | Hard but more prone to shattering upon significant impact. |
Weight | Heavier. | Lighter. |
Cost-Benefit Analysis: Initial Investment vs. Long-Term Savings
While Carbide Ring For Pad Printing Ink Cups carry a higher initial price tag, their extended lifespan and superior performance often translate into significant long-term savings. For high-volume operations, the reduced downtime for ring changes and the consistent production of high-quality prints can lead to a strong return on investment (ROI) that quickly offsets the initial cost. Conversely, ceramic rings are more appealing for lower-volume applications or for those with tighter initial budgets where the slight compromise in lifespan is acceptable.
Common User Questions & Solutions
Here are some frequently asked questions from users in need of Carbide Ring For Pad Printing Ink Cups, along with expert solutions:
- “My current rings wear out too fast. Which material should I choose?”
- Solution: If you’re experiencing rapid wear, especially in high-volume production or when using abrasive inks, carbide is undoubtedly the superior choice. The exceptional durability of a Carbide Ring For Pad Printing will drastically extend replacement cycles and improve overall efficiency.
- “I’m on a tight budget. Is ceramic good enough?”
- Solution: Yes, ceramic rings are a perfectly viable and cost-effective option for lower to medium volume applications or when using non-abrasive inks. They still offer significant improvements over traditional steel doctoring blades and can provide excellent print quality within their operational lifespan.
- “How do I prevent my rings from chipping?”
- Solution: Both carbide and ceramic rings, despite their hardness, require careful handling. Always ensure they are installed and removed gently, avoiding any forceful contact with hard surfaces. Proper storage when not in use, protecting them from drops or impacts, is also crucial. Regular machine maintenance, ensuring proper ink cup alignment and pressure, can also minimize stress on the rings.
- “Does the ring material affect ink consumption?”
- Solution: Indirectly, yes. A precisely doctored ink cup, maintained by a durable and consistently sharp ring (like carbide), ensures the optimal amount of ink is picked up. This reduces ink waste and optimizes ink usage, leading to more cost-effective printing. A worn or imprecise ring can lead to excess ink on the plate, causing smudging and increased consumption.
- “What’s the best way to clean these rings?”
- Solution: For both carbide and ceramic rings, gentle cleaning with appropriate solvents for your ink type is recommended. Use soft, lint-free cloths and avoid abrasive materials or harsh chemicals that could damage the surface. Always refer to the Carbide Ring For Pad Printing manufacturers or Carbide Ring For Pad Printing suppliers guidelines for specific cleaning instructions.
Making the Right Choice for Your Application
Choosing between carbide and ceramic ultimately comes down to a careful evaluation of your specific operational needs and priorities. Consider the following:
- Production Volume: For high-volume, continuous production where maximizing uptime is critical, the superior longevity and consistency of a Carbide Ring For Pad Printing make it the optimal choice.
- Ink Type: If you frequently use abrasive or highly pigmented inks, carbide’s wear resistance will provide a significant advantage in maintaining print quality and extending ring life.
- Budget & Long-Term Goals: While ceramic offers a lower initial cost, consider the long-term operational expenses. For many professional users, the ROI on carbide, driven by reduced downtime and consistent quality, often justifies the higher initial investment. Look for reputable Carbide Ring For Pad Printing factory direct options for competitive pricing and quality assurance.
- Handling & Maintenance Practices: If your environment is prone to accidental drops or impacts, you might need to weigh the brittleness factor, though proper handling should always be prioritized.
Conclusion
Both carbide and ceramic rings offer distinct advantages for pad printing ink cups. Carbide rings stand as the pinnacle of performance and durability, providing unmatched longevity, superior print quality, and reduced operational costs for demanding, high-volume applications. Ceramic rings, conversely, offer a compelling balance of good performance and cost-effectiveness, making them an excellent choice for lower-volume operations or those with budget constraints.
Ultimately, the “best” choice is the one that aligns perfectly with your specific production volume, ink types, budget, and long-term printing goals. By carefully assessing these factors and considering the insights provided by Carbide Ring For Pad Printing manufacturers and Carbide Ring For Pad Printing suppliers, you can select the ideal doctoring ring material to optimize your pad printing process and achieve consistent, high-quality results.