In the world of manufacturing and customization, the choice of a pad printing machine is a critical decision that directly impacts product quality and production efficiency. As a potential buyer, understanding the factors that influence selecting the appropriate machine size and configuration is essential.
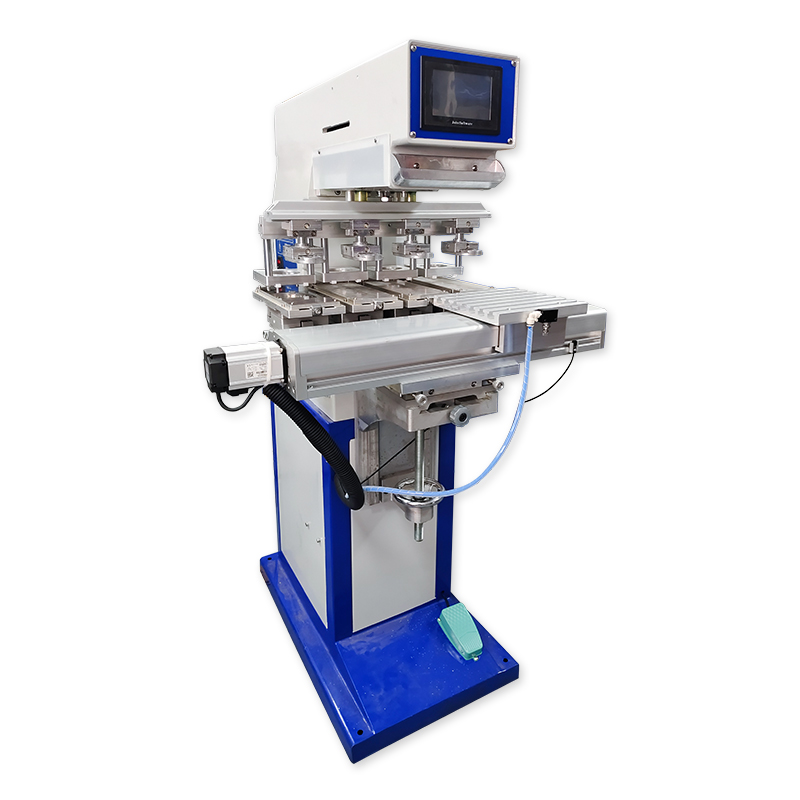
Understanding the Basics of Pad Printing
Before delving into the factors that guide your choice, it’s essential to have a solid grasp of pad printing. Pad printing, often called tampon printing, is a versatile process for applying images, logos, and other markings to various surfaces. It’s widely employed in electronics, automotive, medical devices, and promotional products. Choosing a suitable pad printer is pivotal in achieving the desired print quality.
Factors Influencing Machine Size Selection
- Type of Products or Substrates: The first consideration when choosing a pad printing machine is the type of products or substrates you plan to print on. Are you dealing with flat surfaces, irregular shapes, or cylindrical objects? Different products may require specific machine configurations to achieve optimal results.
- Production Volume and Throughput Requirements: The volume of items you need to print plays a crucial role in machine selection. A high-volume production environment demands a different size and configuration than low-volume custom printing.
- Available Workspace and Layout Constraints: Your workspace and layout constraints are vital in determining the size and layout of the machine. Measure the open space to ensure the selected pad printing machine fits comfortably.
Configurations for Specific Applications
Once you’ve considered the fundamental factors, such as the type of products, production volume, and workspace constraints, it’s time to delve into the machine configurations best suited for your specific applications.
Pad printing machines come in various configurations, but two primary types dominate the market: closed-cup and open-inkwell configurations.
Closed-Cup Configuration
In the closed-cup configuration, the ink cup covers the entire inkwell. This design offers several advantages, including:
- Ink Consistency: The closed cup design helps maintain ink consistency, reducing the risk of ink drying or contamination.
- Clean Printing: It minimizes exposure to fumes and solvents, making it a preferred choice for cleanroom environments.
- Less Ink Waste: Ink is contained within the cup, reducing ink waste and making it more cost-effective.
This configuration is often ideal for small to medium-sized production runs with fine details and strict quality requirements.
Open-Inkwell Configuration
On the other hand, the open-inkwell configuration offers its own set of advantages:
- Faster Setup: It allows for quick colour changes, making it suitable for projects requiring frequent ink changes.
- Versatility: It’s adaptable to various ink types and formulations.
- High-Volume Capability: This configuration is favoured for high-volume production as it can hold a larger volume of ink.
Selecting between the closed-cup and open-inkwell configurations depends on your specific printing needs and the factors we discussed earlier. Consider the type of products you are printing, the required print quality, and the production volume.
Ink Compatibility and Print Quality
Choosing the correct type of ink for your pad printing machine is paramount to achieving the desired print quality. The type of ink you select must be compatible with your machine’s configuration and the specific substrates you are printing on.
- Ink Types: Different inks are formulated for various applications. For instance, solvent-based inks are suitable for adhesion to plastic substrates, while UV-curable inks are ideal for rapid curing and adherence to multiple materials. Water-based inks may be more environmentally friendly but have specific requirements.
- Machine Configuration: The ink you choose should align with your machine’s configuration. Closed-cup engines work well with solvent-based inks, while open-inkwell machines accommodate a broader range of ink types.
- Substrate Compatibility: Consider the nature of the substrates you are printing on. Are they porous or non-porous? Do they have unique surface characteristics? The ink’s adhesion and drying properties should match the substrates.
- Print Quality and Durability: Assess the desired print quality and durability. Some inks are better suited for intricate, high-resolution graphics, while others excel in industrial applications where durability is critical.
By understanding the relationship between ink compatibility and print quality, you can make an informed decision that aligns with your specific pad printing requirements.
Automation and Additional Features
In today’s fast-paced manufacturing environments, automation and additional features in a pad printing machine can significantly improve efficiency and consistency. Depending on your specific application, you may need to consider the following:
- Automation Levels: Some pad printing machine manufacturers offer varying levels of automation. Automated loading and unloading of products, as well as robotic systems for ink application, can streamline production and reduce the need for manual labour.
- Multiple Color Stations: If your application involves multi-colour printing, consider a machine with various colour stations. This allows you to apply different colours in a single pass, saving time and ensuring colour consistency.
- Custom Tooling: For unique or irregularly shaped products, having the ability to create custom tooling and fixtures can be a game-changer. Check if the machine you are considering offers this option.
- Data Integration: In the era of Industry 4.0, the ability to integrate your pad printing machine with data systems and analytics can provide valuable insights into your production process. Consider the machine’s compatibility with data integration solutions.
When selecting a machine with automation and additional features, it’s essential to weigh the benefits against the added cost and complexity. Customizing your device to meet your needs can be a wise investment in the long run.
Cost Considerations
Selecting the suitable pad printing machine involves more than just the initial purchase cost. You should also factor in the total cost of ownership, including maintenance, ink, and any ongoing expenses related to machine operation. Here are some key cost considerations:
- Initial Investment: Assess the initial purchase cost of the machine. Remember that high-quality, feature-rich devices may come with a higher upfront cost.
- Ink and Consumables: Different inks and consumables have varying costs. Consider the ongoing expense of ink replenishment, pads, and other consumables.
- Maintenance Costs: Regular maintenance is essential to keep your machine running smoothly. Evaluate the maintenance requirements and associated costs.
- Energy Efficiency: A more energy-efficient machine can lead to long-term cost savings on electricity bills. Consider the energy consumption of the device.
- Training and Support: Ensure you have access to training and technical support from the pad printing machine manufacturer. This can help reduce downtime and improve machine longevity.
- Scalability: Consider your future needs. Investing in a machine that can scale with your business may be cost-effective in the long run.
By evaluating the full spectrum of costs associated with your pad printing machine, you can make a well-informed decision that aligns with your budget and long-term objectives.
Case Studies
To better understand the practical application of the factors we’ve discussed, let’s explore a few case studies of businesses that have successfully chosen the suitable pad printing machine for their specific needs.
Case Study 1: Custom Promotional Products
Business: A company specializing in customized promotional products, including branded pens, USB drives, and keychains.
Challenge: The business required a pad printing machine capable of handling various products with intricate designs. They opted for an open-inkwell configuration to facilitate quick ink changes for different colours and substrates.
Result: The open-inkwell machine’s versatility allowed efficient printing on various products, meeting their diverse customer demands. It boosted production and increased revenue.
Case Study 2: Medical Device Manufacturer
Business: A medical device manufacturer producing diagnostic test kits and equipment.
Challenge: The company needed a pad printer for applying labels and markings on medical devices. Precision and consistency were critical. They selected a closed-cup configuration to maintain ink consistency and ensure sterile printing.
Result: The closed-cup machine met stringent quality requirements and reduced the risk of contamination in a cleanroom environment. It enhanced the company’s reputation for high-quality, reliable products.
Case Study 3: Automotive Parts Supplier
Business: An automotive parts supplier producing components such as buttons and switches.
Challenge: The business required a high-speed, high-volume pad printing machine for marking automotive parts. They invested in an automated machine with multiple colour stations to meet the demands of their production line.
Result: The automated machine improved production speed, reduced labour costs, and ensured consistent, multi-colour printing on a large scale. It led to increased efficiency and satisfied customers.
These case studies illustrate the importance of aligning machine selection with specific application needs. Learning from these real-world examples can help you decide when choosing a pad printing machine for your business.
Conclusion
Selecting a suitable pad printing machine is a crucial decision that can significantly impact your product quality, efficiency, and long-term costs. To make an informed choice, consider the following key factors:
- Type of Products or Substrates: Determine the nature of the items you’ll be printing on.
- Production Volume and Throughput Requirements: Assess your production needs.
- Available Workspace and Layout Constraints: Measure your open space.
- Ink Compatibility and Print Quality: Choose the right ink type for your applications.
- Machine Configuration: Decide between closed-cup and open-inkwell configurations.
- Automation and Additional Features: Evaluate the benefits of automation and custom tooling.
- Cost Considerations: Look at the total cost of ownership, including maintenance and consumables.
By thoroughly assessing these factors and, if needed, seeking guidance from a pad printing machine manufacturer, you can make a choice that aligns with your unique requirements. Remember that a well-informed decision can lead to increased productivity, better print quality, and, ultimately, more tremendous success in your industry.
For more details or help selecting the ideal pad printing machine, please contact our team of experts..
Thank you for reading, and we wish you success in your pad printing endeavours!