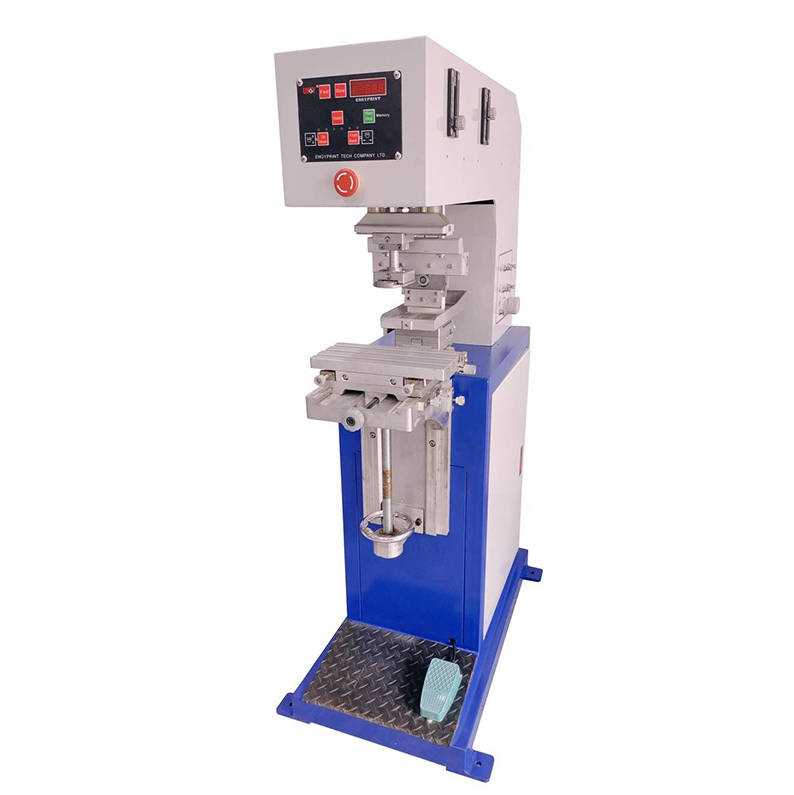
Pad printing has long been recognized as a highly effective technique for printing on curved or complex surfaces. From promotional items to intricate electronic components, this method relies on a silicone pad to transfer ink from an etched plate onto various substrates. In recent years, the rise of UV-curable inks has introduced enhanced possibilities for anyone looking to optimize their pad printing results. These specialized inks cure almost instantly under ultraviolet light, leading to benefits like reduced drying times and improved durability. In this article, I will explore the advantages of UV-curable inks in pad printing and how they elevate overall efficiency, sustainability, and product quality.
[Table of Contents]
- 1. Introduction
- 2. Fundamentals of Pad Printing
- 3. Comparing Traditional Inks and UV-Curable Inks
- 4. Deep Dive into UV-Curable Ink Components
- 5. Advantages of Using UV-Curable Inks
- 6. Industry Applications and Case Examples
- 7. Choosing the Right Pad Printing Equipment
- 8. Common Challenges and Solutions
- 9. Future Trends
- 10. Conclusion
2. Fundamentals of Pad Printing
Pad printing is a versatile process where ink is transferred from a metal or photopolymer plate (cliché) onto a silicone pad, which is then pressed onto the substrate. This indirect offset printing method is particularly useful for printing on surfaces with uneven shapes or textures. Though it seems straightforward, several key elements must work together to achieve precise and vibrant prints.
A typical setup includes a pad printer or pad printing machine, a silicone pad, an ink cup or ink trough, and carefully formulated pad printing supplies like inks and cleaning chemicals. Variations exist, ranging from manual presses to highly advanced automatic pad printing machines that streamline production for large-scale operations. These machines often incorporate advanced features like automated ink feed systems and closed-loop printing controls to ensure consistent results.
Through careful calibration of pad pressure, dwell time, and pad shape, pad printing can replicate fine details on products as diverse as toy parts, automotive interior dials, and even medical devices. The technique’s ability to reach recessed or curved sections sets it apart from other printing methods, making it well-loved in multiple industries.
Why Pad Printing Matters
The flexibility to print on irregular shapes is one of the key drivers behind the popularity of pad printing. While techniques like screen printing also hold their ground for flat surfaces, pad printing can conquer three-dimensional objects. From small promotional trinkets to large industrial parts, the technology accommodates highly detailed print tasks with minimal distortion—an attribute that is especially beneficial when brand consistency and durability are of utmost importance.
3. Comparing Traditional Inks and UV-Curable Inks
Historically, pad printing relied heavily on solvent-based inks that dry through evaporation. While these inks remain widely used and are effective in many scenarios, they come with longer drying times and elevated emissions of Volatile Organic Compounds (VOCs). This can pose both logistical and environmental challenges in high-volume production environments.
In contrast, UV-curable inks utilize a chemical composition that includes photoinitiators. When they’re exposed to UV light, a fast polymerization reaction occurs, converting the liquid ink into a rigid film almost on contact. This transformation slashes the drying time from minutes—or even hours—to seconds. As a result, manufacturers can move printed parts off the production line quicker, enabling higher throughput.
Another benefit lies in the distinct chemical properties of UV inks. With fewer solvents and reduced odor, UV-curable formulations typically produce lower overall emissions. For facilities looking to meet stringent environmental regulations, UV-curable inks offer an appealing path forward.
Solvent-Based vs. UV-Curable
- Drying Method: Solvent-based inks rely on evaporation, while UV-curable inks solidify under UV exposure.
- Production Efficiency: UV inks allow for nearly instantaneous curing, reducing bottlenecks.
- Environmental Impact: Less VOC emission in UV-curable inks contributes to a more eco-friendly operation.
However, it’s worth noting that UV-curable systems generally require specialized pad printing equipment with built-in UV lamps or external curing units. This initial capital outlay can be higher, but the efficiency gains often justify the initial cost over time.
4. Deep Dive into UV-Curable Ink Components
The power of UV-curable inks stems from a deliberate interplay among their core components. Three major constituents stand out: monomers, oligomers, and photoinitiators. Together, they govern everything from curing speed to final film hardness and flexibility.
1. Monomers
Monomers are small, reactive molecules that link up to form polymers once exposed to UV light. They contribute to attributes like viscosity and the molecular structure of the printed layer. Choosing the right monomer can drastically affect the ink’s overall coverage and cure time.
2. Oligomers
Oligomers are larger molecules than monomers, often pre-polymerized to a degree. They define bulk properties such as hardness, elasticity, chemical resistance, and gloss. By tweaking oligomer types or ratios, ink formulators can customize the end properties for specific applications—e.g., flexible electronics or rigid automotive components.
3. Photoinitiators
Photoinitiators absorb the energy from UV light and jumpstart the polymerization process. The choice of photoinitiator also influences the wavelength range required for curing. Efficient photoinitiators ensure the ink cures thoroughly, leaving minimal tack or uncured residue that could compromise print quality.
Balancing these components is a fine art. Ink suppliers run rigorous tests to achieve the desired balance of fluidity, stability, color brilliance, and cure speed. An automatic pad printing machine that uses UV inks typically integrates a UV lamp, ensuring a precise dose of UV light at the right stage of ink transfer and substrate contact.
5. Advantages of Using UV-Curable Inks
UV-curable inks offer a host of benefits that address core challenges in the pad printing process. Below, I highlight some of the most compelling advantages, ranging from faster production cycles to more robust environmental compliance.
1. Faster Production Throughput
In manufacturing, time is money. With UV-curable inks, the final print solidifies within seconds under UV light, eliminating prolonged dry times. This immediate curing capability smooths line efficiencies, particularly in continuous or large-scale runs. Whether you have one pad printer handling short batches or a high-capacity automatic pad printing machine running 24/7, the uptick in productivity can be dramatic.
2. Enhanced Ink Durability and Aesthetics
Once cured, UV inks tend to exhibit excellent adhesion and form a tough surface. This resilience helps withstand scuffs, chemical exposure, and general wear over time. Moreover, the quick lock-in of color particles typically ensures vibrant hues that remain consistent through frequent handling. In highly regulated industries, such as automotive or medical, these properties reduce the chance of print failure and ensuing scrap rates.
3. Reduced VOCs and Environmental Benefits
Environmental standards continue to tighten globally, compelling manufacturers to investigate greener printing options. UV-curable inks contain minimal volatile components and release fewer airborne pollutants, making them appealing for facilities seeking to reduce their ecological footprint. In addition, operators may appreciate the reduced smell and safer working environment that these inks often provide.
4. Versatility on a Wide Range of Substrates
UV-curable inks are well-suited for many substrates—metals, plastics, glass, and even composites. This opens doors for cross-industry use in electronics, cosmetics packaging, promotional goods, and more. By adjusting the specific formulation—particularly the blend of oligomers and monomers—ink manufacturers cater to a multitude of specialty applications, making it simpler for companies to adopt a single solution across diverse product lines.
5. Potential for Automation and Cost-Saving
The instantaneous curing nature of UV inks lends itself well to automated setups. When coupled with a modern pad printing machine or, more specifically, an automatic pad printing machine, you can program precisely controlled passes beneath the UV lamp to lock in quality consistently. Near-instant curing contributes to a streamlined workflow where components move swiftly from one stage to another, cutting factory floor congestion.
6. Industry Applications and Case Examples
While UV-curable inks have the potential to elevate almost any pad printing process, they shine particularly bright in specific industries. Below are some standout examples.
Automotive
Modern vehicles feature numerous interior and exterior components that require crisp, long-lasting markings or decorative designs. From dashboard symbols to center-console icons, the longevity of UV ink ensures these prints maintain clarity under sunlight, temperature swings, and the wear that occurs through everyday driving.
Electronics
Electronic devices often have intricate shapes, requiring printing in tight corners and on multi-dimensional surfaces. Combining UV-curable inks with an advanced pad printing machine solves these challenges and produces consistent, durable markings. For instance, mobile phone accessories, game controllers, and wearable sensors rely on pad printing to stay visually appealing and functional.
Advertising and Packaging
Brands invest heavily to stand out on shelves. UV-pad printing ensures their logos and messaging appear bright and distinct on items like promotional pens, cosmetic containers, and other packaging components. When speed is key—especially in big promotional campaigns—UV-curable inks help meet demanding deadlines by expediting the entire drying process.
Medical and Laboratory Devices
In medical environments, printed markings must withstand cleaning agents and sterilization processes. UV inks form a robust bond with devices, ensuring that crucial measurement lines or labeling remain intact and legible throughout the product’s lifecycle. This reliability is essential for patient safety and regulatory compliance.
7. Choosing the Right Pad Printing Equipment
Not every pad printing setup is identical. Companies often upgrade their pad printing equipment when deciding to transition to UV-curable inks. Though many older machines can be retrofitted with UV curing modules, purpose-built automatic pad printing machines designed for UV-curable processes typically yield better results.
Key Considerations
• UV Lamp Specifications: The wavelength output must match the photoinitiator in the ink. LED UV systems are growing in popularity due to lower heat emission and energy consumption.
• Software and Automation: For high-volume printing, advanced machines allow you to program precise dwell times and pad movements.
• Ink Compatibility: Consult with ink suppliers to ensure the hardware and formulations align for effective polymerization.
Return on Investment
Although UV-based pad printing equipment can command a higher upfront price, many manufacturers witness a reasonable return on investment through time savings, reduced reprints, and lower rates of product rejection. Additionally, the enhanced print quality and environmental compliance can open doors to new business opportunities that demand cutting-edge printing solutions.
8. Common Challenges and Solutions
Transitioning to UV-curable inks in pad printing isn’t always seamless. Below are some typical issues and proven solutions.
1. Incomplete Curing
If your prints feel tacky or smudge even after UV exposure, it may indicate inadequate exposure time or suboptimal UV lamp intensity. Fine-tuning lamp height, conveyor speed, or dwell intervals typically resolves this hurdle. Regularly monitoring the lamp’s power output helps ensure consistent curing as the lamp ages.
2. Ink Overflow and Blurring
Printing too much ink can lead to bleeding edges or blurred artwork. Adjust the amount of ink that the pad picks up by modifying the doctor blade pressure or the design of your pad printing supplies (e.g., cliche depth). A well-balanced system invests in carefully controlling how each droplet of ink is deposited.
3. Color Inconsistency
Since UV inks polymerize rapidly, any misalignment in pad or substrate handling can lock in partial prints. Ensure that your automatic pad printing machine is calibrated for consistent pressure, speed, and timing. Maintaining stable room ambient conditions, including temperature and humidity, can also help.
4. Substrate Compatibility
Not all materials interact equally with every ink formulation. When implementing a new part or product, test the ink’s adhesion thoroughly. Try multiple pretreatments such as flame treatment or plasma, if necessary, to enhance surface energy and improve bond strength between ink and substrate.
9. Future Trends
As the pad printing sector evolves, so does the technology surrounding UV-curable inks. Within research and development labs, scientists are exploring eco-friendlier photoinitiators and experimenting with novel resin blends that yield functional surfaces with antimicrobial or conductive properties.
Innovations in pad printing equipment are also on the horizon. Expect more automatic pad printing machines with multi-axis control, improved efficiency in ink usage, and integrated sensors that measure or adjust the UV intensity on-the-fly based on real-time feedback. This helps maintain quality across varied substrates and further reduces material waste.
Sustainability is another driving force. Many manufacturers are pushing for even lower VOC inks, biodegradable components, and overall reduced energy consumption throughout the printing process. As a result, we could see pad printing expand into niche markets that demand both robust mechanical performance and minimal environmental footprint.
10. Conclusion
UV-curable inks stand out as a game-changer for modern pad printing, significantly boosting efficiency, end-product quality, and environmental friendliness. By offering near-instant curing and remarkable resilience on a broad spectrum of substrates, these inks simplify complex production demands. Whether operating a single manual press or an advanced network of automatic pad printing machines, integrating UV-curable inks into your existing toolkit can lead to transformative results—raising your throughput and your reputation for quality.
As the industry moves forward, continuous advancements in pad printer design, formulation science, and automation will further expand the capabilities of UV-curable inks, ensuring that pad printing continues to thrive in a rapidly evolving manufacturing landscape.