I. Introduction: Understanding Your Pad Printing Choices
In the dynamic world of product marking, pad printing stands out as a highly versatile and precise technology, capable of transferring intricate designs onto a myriad of irregular surfaces. Yet, beneath the surface of this remarkable process lies a critical choice that significantly impacts performance: the ink delivery system. For businesses striving for consistent quality, operational efficiency, and enhanced safety, the decision between a Closed Ink Cup system and an Open Ink Well system is paramount.
This guide is specifically tailored for those who are either considering, or already leaning towards, the myriad advantages of the Closed Ink Cup system. We’ll delve into its mechanics, explore its compelling benefits, and address common questions, helping you navigate your pad printing future with confidence. Our aim is to provide clarity and demonstrate why the Closed Ink Cup is often the superior choice for demanding applications.
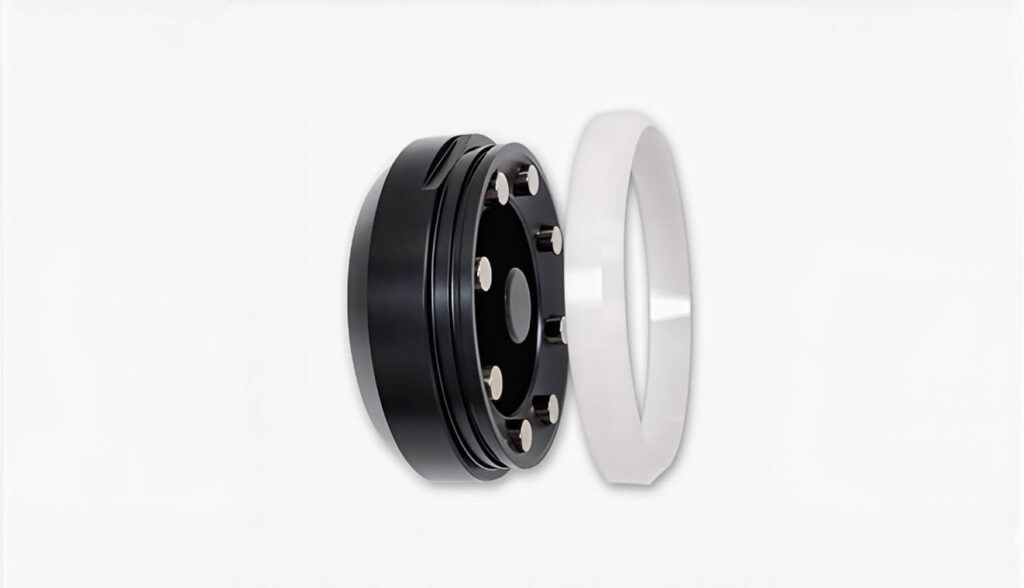
II. Demystifying the Closed Ink Cup System: Core Principles and Advantages
At its heart, the Closed Ink Cup system is a marvel of engineering designed to optimize ink control. Unlike the exposed ink in an open well, the Closed Ink Cup operates as a sealed unit. As the pad descends to pick up ink, the cup slides over the etched cliché (printing plate), filling the engraved image area with ink. A precise doctoring ring, forming the seal with the cliché, then scrapes away excess ink, leaving only the required amount in the image. The pad then presses onto the cliché, picking up the image, before transferring it to your product. This elegant, contained process is the foundation of its many benefits.
The advantages of the Closed Ink Cup system are substantial, making it the preferred choice for a wide range of industries:
A. Superior Ink Viscosity Control & Consistency
One of the most significant benefits of a Closed Ink Cup is its ability to maintain ink integrity. Because the ink is sealed within the cup, solvent evaporation is drastically reduced. This minimizes changes in ink viscosity over time, leading to remarkably stable print quality, even during extended production runs. Operators spend less time monitoring and adjusting ink, ensuring consistent color, opacity, and detail from the first print to the last. This consistency is invaluable for brands where precise color matching and sharp graphics are non-negotiable.
B. Enhanced Operator Safety & Environmental Benefits
The sealed nature of the Closed Ink Cup system offers considerable improvements in workplace safety and environmental impact. By containing ink and solvents, the release of volatile organic compounds (VOCs) into the atmosphere is significantly minimized. This reduces operator exposure to potentially harmful fumes, creating a healthier working environment. For wholesale Closed Ink Cup operations, this not only safeguards personnel but also helps in complying with increasingly stringent environmental regulations, making your facility greener and safer.
C. Material & Cost Efficiency
While the initial investment in a Closed Ink Cup machine might be perceived as higher, the long-term cost savings are compelling. The reduced solvent evaporation means less ink waste and lower solvent consumption for thinning and cleaning. This directly translates to substantial savings on consumables over the machine’s lifespan.
D. Cleaner Operations & Reduced Contamination
Imagine a pad printing environment where mess is minimized and contamination risks are dramatically lowered. This is the reality with a Closed Ink Cup system. The ink is fully contained within the cup, preventing spills, splashes, and airborne dust or debris from entering the ink supply. This clean operation is particularly critical for industries like medical device manufacturing, electronics, and automotive, where even microscopic contaminants can compromise product quality. Leading Closed Ink Cup manufacturers design their systems with this level of cleanliness in mind, ensuring pristine results.
E. Easier Setup & Quicker Changeovers
Streamlining production is vital in today’s fast-paced manufacturing landscape. Closed Ink Cup systems contribute significantly to this by simplifying setup and accelerating changeovers. Ink is typically pre-measured and contained within the cup, eliminating the need for manual ink pouring and messy adjustments. Plate changes are also quicker, as there’s less concern about ink spillage. This reduced downtime means higher throughput and increased productivity for your operations.
F. Versatility for Various Applications
The controlled environment of the Closed Ink Cup system allows it to handle a wider array of ink types and viscosities more effectively. Whether you’re working with fast-drying inks for high-speed production or specialized inks for challenging substrates, the consistent viscosity control ensures optimal performance. This versatility makes the Closed Ink Cup system a robust solution for diverse pad printing applications, from delicate cosmetic packaging to robust industrial components. Many reputable Closed Ink Cup suppliers offer a range of cup sizes and materials to accommodate virtually any printing requirement.
III. Addressing Common Questions and Misconceptions for Closed Ink Cup Users
Despite its clear advantages, potential users often have questions or harbor misconceptions about the Closed Ink Cup system. Let’s address some of these head-on:
A. “Is the initial investment higher?”
It’s true that the upfront cost of a Closed Ink Cup machine can sometimes be higher than a basic open ink well system. However, this is a classic case of short-term cost versus long-term value. When you factor in the ongoing savings from reduced ink and solvent consumption, lower labor costs due to less cleanup and fewer adjustments, and significantly fewer rejected parts due to inconsistent quality, the return on investment (ROI) quickly becomes evident. Many businesses find that the initial outlay is recouped within a surprisingly short period.
B. “Is maintenance more complex?”
Paradoxically, maintenance for a Closed Ink Cup system is often simpler and less time-consuming. While the doctoring ring and cup need proper care, the absence of an open ink reservoir means there’s no need to clean large, exposed ink trays or deal with dried ink messes. Routine cleaning of the cup and doctoring ring is typically straightforward, contributing to less overall maintenance downtime.
C. “What about print size limitations?”
A common concern revolves around the idea that Closed Ink Cup systems are limited to smaller print areas. While it’s true that the cup’s diameter dictates the maximum print area, Closed Ink Cup manufacturers produce a wide range of cup sizes, from small cups for intricate details to very large cups (up to 200mm or more in diameter) capable of printing substantial images. If your application requires a large print, there’s likely a Closed Ink Cup machine designed to accommodate it.
D. “Can it handle all ink types?”
Generally, yes. Due to its superior control over ink viscosity and evaporation, the Closed Ink Cup system is highly adept at handling various ink types, including those that might be challenging in an open system, such as fast-drying or highly pigmented inks. The contained environment helps prevent premature drying of the ink, which is a common issue in open wells, especially with solvent-based inks.
E. “How does it impact production speed?”
While the initial ink loading mechanism might appear different, the consistent performance of the Closed Ink Cup system often leads to higher effective production speeds. Because operators don’t need to frequently stop and adjust ink viscosity or clean up messy spills, the overall operational uptime is increased. This consistency translates directly to more parts printed per hour with fewer quality deviations.
IV. Choosing the Right Closed Ink Cup System: Key Considerations
Selecting the ideal Closed Ink Cup system for your operations requires careful consideration of several factors:
- Cup Diameter and Image Size: Ensure the cup diameter is appropriate for the largest image you intend to print, with some margin for error. Consult with Closed Ink Cup suppliers to match cup sizes to your specific graphic requirements.
- Automation Level: Pad printing machines range from manual benchtop units to fully automated, integrated systems. Your production volume, labor availability, and required throughput will dictate the appropriate level of automation.
- Machine Features: Consider the number of colors you need, whether a shuttle or rotary system is more suitable for your parts, and if features like automatic pad cleaning, parts handling, or vision systems are beneficial.
- Material Compatibility: Verify that the materials of the ink cup and doctoring ring are compatible with the specific inks and solvents you plan to use to ensure longevity and optimal performance.
- Supplier Support and Training: Partnering with reputable Closed Ink Cup manufacturers or suppliers who offer excellent technical support, readily available spare parts, and comprehensive operator training is crucial for long-term success.
V. Conclusion: Making an Informed Decision for Your Pad Printing Future
For businesses that prioritize precision, consistency, operator safety, and long-term cost efficiency in their pad printing operations, the Closed Ink Cup system emerges as the clear frontrunner. Its innovative design minimizes ink waste, reduces VOC emissions, simplifies cleanup, and delivers unparalleled print quality stability.
By investing in a Closed Ink Cup system, you’re not just buying a machine; you’re investing in a more efficient, safer, and ultimately more profitable pad printing future. Evaluate your specific production needs, consider the long-term benefits, and confidently choose the system that aligns with your pursuit of operational excellence.