Choosing the right printing technology is a critical decision that directly impacts your product’s quality, durability, and production efficiency. For businesses considering a pad printing machine, understanding its unique strengths in comparison to other printing methods, especially UV printing, is essential. This article dives deep into the nuances of pad printing vs. UV printing, comparing their durability, speed, and substrate compatibility, to help you make an informed choice for your specific manufacturing requirements.
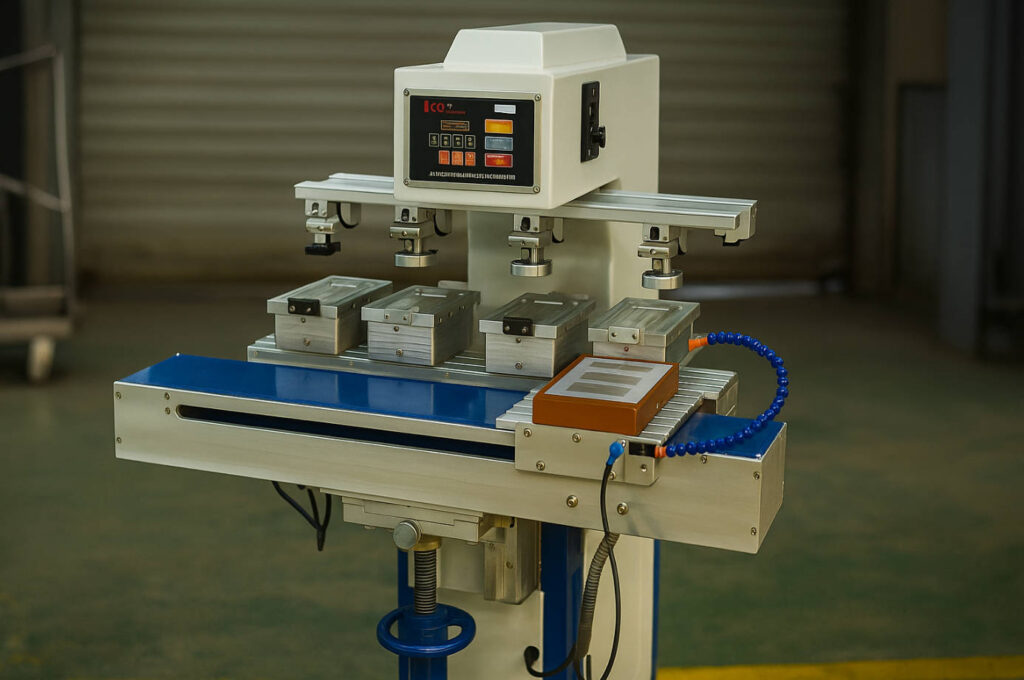
Understanding Pad Printing Technology
Pad printing, a highly versatile and precise printing method, utilizes an indirect offset (gravure) printing process. It involves transferring an image from an etched printing plate (cliché) via a silicone pad onto a substrate. The image, which is etched into the cliché, is filled with ink. The silicone pad then presses onto the cliché, picks up the ink, and finally transfers it onto the object. This unique process allows for printing on surfaces that are difficult or impossible for other methods to handle.
The advantages of a pad printing machine are numerous, making it a staple in many industries. Its most notable benefit is its unparalleled ability to print on irregular, curved, textured, and even spherical surfaces. The deformable silicone pad effortlessly conforms to various shapes, ensuring high-quality, crisp images on challenging geometries. Furthermore, pad printing excels in achieving exceptional precision and fine detail, making it ideal for small graphics, intricate logos, and micro-printing on compact components. For many applications, particularly those involving a limited number of colors or high volumes of smaller items, it can also be a cost-effective solution due due to lower ink consumption and simpler setup compared to some digital methods. The inks used in pad printing, such often solvent-based or two-part epoxy inks, are renowned for their excellent adhesion and durability, forming a strong bond with the substrate, making them suitable for high-wear products.
Common applications where you’ll find a pad printing machine in action include medical devices (syringes, catheters), automotive parts (buttons, dials), promotional items (pens, stress balls), electronic components (keyboards, circuit boards), and sporting goods (golf balls, helmet padding). When sourcing your equipment, look for a reputable pad printing machine factory or pad printing machine manufacture to ensure quality and reliability.
Exploring UV Printing Technology
UV printing is a form of digital inkjet printing that uses ultraviolet (UV) lights to cure or dry ink as it is printed. As the printer distributes ink on the surface of a material (substrate), specially designed UV lights follow closely behind, instantly curing the ink. This immediate curing process results in a durable, vibrant print that is ready for immediate use.
UV printing offers several compelling advantages. Perhaps its biggest draw is the instant curing, which translates to high production speeds and eliminates the need for drying time. This “print-and-go” capability significantly streamlines production workflows. UV inks are known for producing vibrant colors and allowing for intricate, photographic-quality graphics, including the ability to print white ink and even clear varnish for tactile effects. Additionally, UV printing boasts broad substrate compatibility, enabling it to print on a wide range of materials such as plastics, glass, wood, metal, and ceramics, often without extensive pre-treatment. However, its compatibility with highly irregular shapes is more limited compared to pad printing, as it primarily works best on flat or slightly curved surfaces.
Typical applications for UV printing include flatbed printing for signs and banners, promotional products with flat surfaces (e.g., USB drives, phone cases), industrial parts with minimal curvature, and custom packaging.
Head-to-Head Comparison: Pad Printing vs. UV Printing
Feature | Pad Printing | UV Printing |
Durability | Excellent adhesion and abrasion resistance, especially with specialized inks (e.g., 2-part epoxies). Forms a strong mechanical and chemical bond. Suitable for high-wear items. | Hard, scratch-resistant cured ink layer. Can be brittle on flexible materials, potentially leading to chipping. |
Speed & Throughput | Good for high-volume, single or few-color jobs. Cycle times can vary. | Instant curing allows for very high production speeds, especially for multi-color and variable data. |
Substrate Geometry | Superior for highly irregular, curved, textured, and 3D objects. Pad conforms to shapes. | Best for flat or slightly curved rigid and flexible substrates. Limited on complex 3D shapes. |
Color Capabilities | Primarily spot colors, excellent opacity on dark backgrounds, precise color matching. | Full CMYK + White + Varnish capabilities, photographic quality, gradients. |
Artwork Complexity | Ideal for logos, text, fine lines, and small details. | Excellent for complex graphics, photos, and variable data printing. |
Setup & Flexibility | Requires cliché plate per design, pad selection. Can be quick for repeat jobs. | Digital, less setup for design changes, ideal for short runs and customization. |
Initial Investment | Generally lower for entry-level machines. | Often higher due to advanced digital technology and UV curing systems. |
Durability
When it comes to durability, both technologies offer robust solutions, but their strengths lie in different areas. Pad printing, particularly with the use of solvent-based or two-part epoxy inks, creates a print that is highly resistant to abrasion, chemicals, and environmental factors. The ink effectively bites into and adheres to the substrate, forming a strong mechanical and chemical bond, which is crucial for parts that undergo constant handling or exposure to harsh conditions. This makes it an excellent choice for medical instruments, automotive components, and industrial parts where longevity is paramount.
UV printing, on the other hand, produces a print with a hard, cured ink layer that is generally scratch and scuff-resistant. However, because the ink sits on top of the substrate, rather than deeply bonding with it, it can be susceptible to chipping or cracking if the underlying material is flexible or subject to significant bending or impact. For instance, a print on a flexible plastic that is frequently bent might show signs of cracking over time.
Speed and Throughput
UV printing undeniably holds an advantage in terms of raw speed and throughput, thanks to its instant curing process. As soon as the ink is jetted onto the substrate, the UV lights cure it immediately, allowing for immediate handling and subsequent production steps. This is particularly beneficial for large runs of multi-color graphics and for applications requiring variable data printing.
While pad printing machines may not offer the same “instant-dry” benefit, their speed is highly efficient for specific tasks. For high-volume production of single-color or few-color designs, modern automated pad printers can achieve impressive cycle times. The speed also depends on the complexity of the part and the number of colors being printed. A well-optimized pad printing machine factory can demonstrate how their equipment performs efficiently in your specific high-volume scenarios.
Substrate Compatibility and Geometry
This is arguably the most significant differentiator. Pad printing reigns supreme when it comes to printing on three-dimensional objects, irregular shapes, and textured surfaces. The flexible silicone pad is designed to conform to almost any shape, including concave, convex, spherical, and even highly textured items. This makes it the go-to solution for printing on golf balls, medical tubing, electronic enclosures with varied contours, and bottle caps. If your product is not flat, a pad printing machine supplier will likely recommend this method.
UV printing, while versatile across a wide range of materials (plastics, glass, metal, wood, ceramic), works best on flat or slightly curved surfaces. While some cylindrical or slightly irregular objects can be printed using rotary attachments, UV printing struggles with complex 3D geometries or deep textures. The digital print heads require a relatively consistent distance from the substrate to ensure proper ink jetting and curing.
Color Capabilities and Artwork Complexity
For color, UV printing offers unparalleled flexibility. It typically utilizes a CMYK (Cyan, Magenta, Yellow, Black) ink set, often augmented with white ink and clear varnish. This allows for full-color photographic quality prints, intricate gradients, and even raised textures or gloss effects. It’s the ideal choice for designs with complex artwork, many colors, or variable data.
Pad printing traditionally uses spot colors, meaning each color is mixed to a specific Pantone shade and applied individually. While this offers excellent color matching and opacity, especially on dark backgrounds, it’s not designed for photographic reproduction or intricate gradients with many colors. However, for crisp logos, text, and precise brand color reproduction, pad printing excels.
Investment and Operational Costs
The initial investment for a pad printing machine is generally lower than for a high-end UV printer, especially for entry-level or semi-automatic models. Operational costs involve cliché plates (etching plates), ink, and silicone pads. These consumables are relatively inexpensive and have a good lifespan. Maintenance on a pad printer is also typically straightforward. Many a pad printing machine manufacture can provide detailed cost breakdowns.
UV printers, being advanced digital machines, often have a higher initial price tag. Operational costs include UV-curable inks (which can be more expensive per liter than pad printing inks) and UV lamp replacement. However, their speed and versatility for variable data can lead to higher overall production efficiency for certain applications, potentially offsetting the higher initial cost in the long run.
When to Choose a Pad Printing Machine: Addressing User Needs
For those actively seeking a pad printing machine, here are the scenarios where it is unequivocally the superior choice:
- You need to print on highly irregular, curved, or textured surfaces. If your product isn’t flat, pad printing is your answer.
- Your primary concern is ink durability and abrasion resistance for components exposed to wear and tear.
- You require precise, detailed printing on small areas or tiny components where legibility is critical.
- You are primarily printing spot colors, solid logos, or designs with a limited number of colors where exact color matching is paramount.
- You are looking for a cost-effective solution for specific high-volume, single-color or two-color applications where consistent quality is key.
- You are working with materials that benefit from a strong, deep ink adhesion, such as certain plastics, metals, or glass.
A common misconception is that “pad printing is slower than UV printing.” While UV printing offers instant curing, pad printing’s efficiency shines in its ability to quickly apply precise, durable prints on challenging geometries, making it incredibly efficient for its niche applications. Another misunderstanding is “can pad printing achieve full-color?” While not suited for photographic full-color, it excels at vibrant, opaque spot colors, which are often preferred for branding. Finally, “is pad printing outdated?” Absolutely not. Pad printing machines continue to be indispensable in industries where other methods simply cannot deliver the required quality or precision on complex parts. Leading pad printing machine suppliers constantly innovate to improve efficiency and capability.
Conclusion
Both pad printing and UV printing are powerful technologies, each with distinct advantages. The “best” choice is not universal; rather, it hinges entirely on your specific application requirements.
If your products feature complex geometries, require extreme ink durability, or demand micro-precision on challenging surfaces, then investing in a pad printing machine is likely your optimal path. It offers a unique capability that no other printing method can fully replicate. Conversely, if your primary needs are flatbed printing, high-speed multi-color production, or variable data printing on mostly flat surfaces, UV printing will serve you better.
Carefully evaluate your product’s shape, the desired print durability, production volume, color requirements, and overall budget. Don’t hesitate to consult with experts from a reputable pad printing machine factory or pad printing machine supplier to get a personalized assessment and ensure you choose the printing solution that best aligns with your business goals.