Pad printing, a versatile and widely used printing technique, is highly valued in industries where high-precision prints on complex and varied surfaces are required. Whether you’re printing on small items like promotional products, electronic components, or large, curved surfaces like automotive parts, ensuring consistent ink flow and viscosity is paramount to achieving top-quality results. For businesses or individuals considering the purchase of a pad printing machine, understanding the role of ink flow and viscosity in the process is crucial for making an informed decision. This article will address the common challenges associated with ink flow and viscosity in pad printer systems and provide actionable solutions to ensure consistent results.
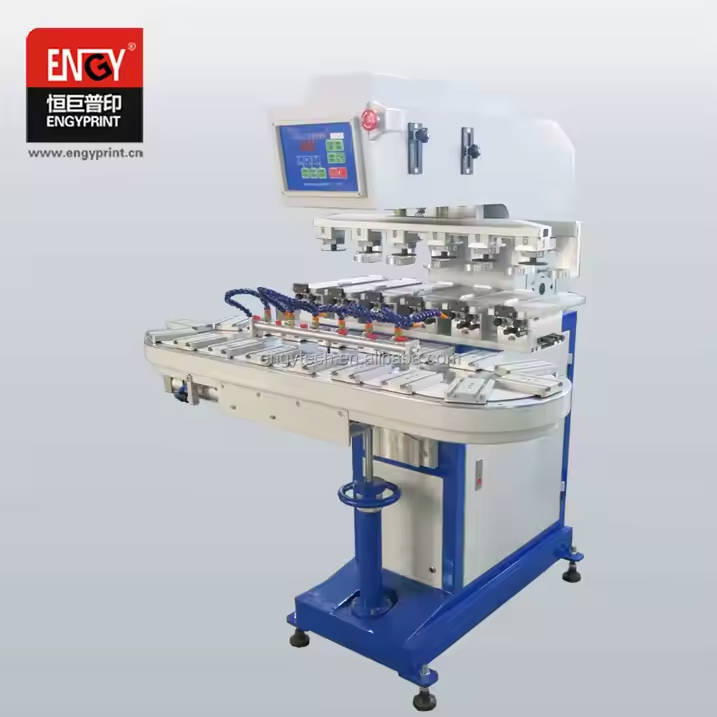
1. The Importance of Consistent Ink Flow and Viscosity
When it comes to pad printing, achieving high-quality results depends on many factors, but none are more critical than the consistency of ink flow and viscosity. The ink used in pad printing must flow smoothly and consistently throughout the entire printing process to ensure uniform coverage and sharp, clear prints. If the ink viscosity is too high or too low, or if the flow is inconsistent, the final print quality can suffer, leading to defects like smudging, uneven ink distribution, or poor adhesion to the substrate.
In addition, the proper ink flow ensures that the ink is evenly transferred from the printing plate to the pad, and ultimately to the surface being printed. Without consistent ink flow, it’s impossible to achieve fine details, sharp edges, or accurate color reproduction—key factors in producing high-quality prints. This is why investing in a high-quality pad printing machine and carefully maintaining ink flow and viscosity is vital for businesses that rely on pad printing.
2. Factors Affecting Ink Flow and Viscosity in Pad Printing Systems
Several factors can influence the ink flow and viscosity in pad printing machines, and understanding these factors is essential for ensuring optimal performance. Below are some of the most important variables to consider:
2.1 Ink Quality and Composition
The quality of the ink used in a pad printing machine plays a significant role in the consistency of ink flow and viscosity. Inks with inconsistent formulations or low-quality components may result in poor adhesion, smudging, or inaccurate color reproduction. High-quality inks are designed to provide consistent flow and viscosity, helping ensure a smooth and reliable printing process.
Moreover, the type of ink—whether solvent-based, water-based, or UV-cured—can also impact viscosity. Different inks have different flow characteristics, and it’s crucial to choose an ink that is compatible with your pad printing machine and the substrates you’re working with. For instance, UV inks often require specialized equipment and curing systems, while solvent-based inks may be prone to drying too quickly, affecting ink flow.
2.2 Ink Viscosity Adjustments
Ink viscosity refers to the thickness or resistance to flow of the ink. If the viscosity is too high, the ink may not transfer well from the plate to the pad, leading to poor prints with insufficient detail. If the viscosity is too low, the ink may spread too much on the substrate, resulting in smudging and blurred lines.
Maintaining the correct ink viscosity is essential for achieving consistent results. Many pad printing machines feature an ink viscosity control system, which allows operators to adjust the ink thickness as needed. For example, some pad printing machines allow you to control the amount of solvent or thinner mixed with the ink to reduce viscosity, while others come with automatic viscosity controllers for easier management.
2.3 Ink Cup and Doctor Blade Functionality
The ink cup is a critical component of the pad printing machine that holds the ink and ensures it is evenly distributed across the plate. The doctor blade, which sits inside the ink cup, is responsible for scraping excess ink from the plate after it has been transferred to the pad, ensuring that the plate has a uniform layer of ink.
Both the ink cup and doctor blade must be well-maintained and properly aligned to ensure smooth ink flow. If either component is damaged, misaligned, or worn out, it can cause ink flow irregularities. Regular cleaning and replacement of these pad printer supplies are crucial for ensuring consistent ink flow.
2.4 Environmental Factors
Environmental factors such as temperature and humidity can also impact ink flow and viscosity. Ink tends to thicken in cold environments and thin in warm environments, which can lead to inconsistencies in print quality. Additionally, humidity can affect the ink’s ability to dry properly, particularly in water-based inks.
To mitigate these issues, it’s essential to maintain a controlled environment in your printing area. Installing air conditioning or dehumidifiers can help regulate the temperature and humidity levels, ensuring the ink remains at optimal viscosity for consistent flow and performance.
3. Solutions for Ensuring Consistent Ink Flow and Viscosity
Now that we’ve covered the factors affecting ink flow and viscosity, let’s discuss the steps you can take to ensure optimal ink performance in your pad printing machine.
3.1 Regular Maintenance of the Pad Printing Machine
Routine maintenance is essential to keeping your pad printing machine running smoothly and ensuring consistent ink flow. This includes cleaning and inspecting the ink cup, doctor blade, and other key components for wear and tear. Any buildup of dried ink or debris can disrupt ink flow and affect print quality.
In addition, regular maintenance helps prevent more significant issues like misalignments or breakdowns, which can lead to inconsistent printing results. By keeping your pad printing machine well-maintained, you can avoid disruptions in the ink flow process and prolong the life of your equipment.
3.2 Investing in High-Quality Pad Printer Supplies
Using high-quality pad printer supplies, such as inks, pads, and printing plates, is essential for achieving consistent results. When selecting ink for your pad printer, choose a reputable supplier who offers products specifically designed for pad printing. Premium inks provide better flow characteristics and are less likely to cause print defects or inconsistencies.
Moreover, regularly replacing consumables such as pads and printing plates ensures that the ink flows properly from the plate to the pad and ultimately to the substrate. Worn or damaged pads can affect the ink transfer process, leading to poor-quality prints.
3.3 Monitoring and Adjusting Ink Viscosity
In order to ensure consistent ink flow, it’s essential to monitor and adjust the ink viscosity regularly. Many pad printing machines are equipped with viscosity control systems that make it easier to maintain the ideal ink thickness. Use these systems to monitor viscosity levels and make adjustments as needed.
If your machine doesn’t have automatic viscosity control, you can use viscosity cups or flow cups to manually measure the ink’s thickness. Make sure to regularly check the viscosity, especially when using different types of ink or when environmental conditions change.
3.4 Implementing Environmental Controls
As mentioned earlier, temperature and humidity can significantly affect ink flow and viscosity. By maintaining a stable environment in your printing area, you can reduce the impact of these factors. Use climate control systems to regulate the temperature and humidity to ensure consistent ink performance.
Additionally, make sure that your pad printing machine is stored in a clean, dust-free environment, as contaminants can affect both the ink and the print quality.
4. Conclusion
Ensuring consistent ink flow and viscosity is essential for achieving high-quality, precise prints with your pad printing machine. By understanding the factors that influence ink flow and viscosity, such as ink quality, viscosity adjustments, and environmental conditions, you can take proactive steps to maintain optimal performance. Regular maintenance of your pad printing machine, investing in high-quality pad printer supplies, and monitoring viscosity are all crucial actions to ensure consistent ink transfer and reliable results.
For businesses considering the purchase of a pad printing machine, it’s important to choose a machine that offers the flexibility to adjust ink flow and viscosity. Whether you’re printing on small or large-scale projects, keeping ink flow consistent and viscosity optimized will help you achieve professional, high-quality prints every time.
By following these guidelines, you can ensure that your pad printing machine operates at peak efficiency, ultimately saving time, reducing waste, and delivering outstanding print quality.